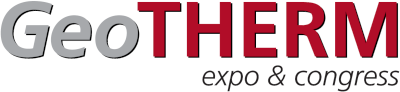
Enhanced and Advanced Geothermal Systems (EGS and AGS) are new methods of creating geothermal installations that have already been demonstrated to potentially increase electric power production by a factor of greater than 10 when compared with more conventional methods. Some involve fracturing the rock between injector and producer wells, and some rely on drilling wells to convey closed loop fluid systems to take heat from the rock.
Many such systems are emerging, with subtly different designs, and they are attracting a lot of funding and excitement. But compared with conventional hydrothermal wells, they are technically challenging to drill. In particular, very accurate well positioning, generally including horizontal wells, will be required for the most advanced well designs to succeed. The oil and gas industry can already drill accurate directional wells and this capability to position the well is potentially directly transferable to some of the first EGS and AGS wells because they are likely to be drilled at temperatures familiar to oil and gas drillers. But to make EGS and AGS wells more economically interesting, they will need to be drilled at higher temperatures which are currently beyond the capabilities of oil and gas drilling, completions, and production equipment.
Even the claimed 175°C operating capability of oil and gas technologies is challenging for the economics of geothermal drilling because equipment operated at this maximum temperature limit exhibits low mean time between failure and/or service. Therefore, the industry needs a step change in its approach to the temperature capabilities of downhole equipment. This presentation will outline just such an approach to the temperature resistance of the electronics and sensors needed.
Showing in detail a new approach to tool design, it will describe how a combination of component selection, a completely reimagined approach to downhole electronics – looking nothing like the boards currently used in oil and gas – and multiple cooling strategies will allow measurement and control to be reliably implemented at higher temperatures, initially above 200°C and ultimately as high as 300°C. This will finally make reliable drilling at high temperature a reality.
The author, John Clegg, has worked for over 37 years with drill bits, drilling motors, Rotary Steerable Systems (RSS), Measurement and Logging While Drilling (MWD and LWD) and Manage Pressure Drilling (MPD), including leading the development of one of the world’s first RSS. John holds a Masters in Engineering Science and a Diploma in Global Business, both from Oxford University. He is a Society of Petroleum Engineers (SPE) Distinguished Lecturer and has sat on the Boards of the Drilling Systems Automation and Research and Development Technical Sections of SPE, the Program Committees for the annual SPE Drilling Conference and the SPE Drilling Advisory Committee. He is now CTO of Hephae Energy Technology, developing high temperature MWD and RSS for geothermal drilling. Hephae Energy Technology will be exhibiting at GeoTherm in 2024.