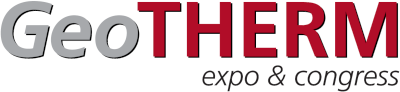
Drilling cost-efficient, safe, and deep wellbores is key to scaling geothermal energy. However, the elevated costs associated with high non-productive and invisible loss times (NPT/ILT) are taxing on the operators, acting as a severe bottleneck in utilizing geothermal energy. In deep geothermal wells, the leading contributors to NPT/ILT are the failure of downhole tools and/or absence of their measurements.
Continuous downhole parameter measurements are often hindered by mud circulation interruptions or downhole tool failures caused by high operating temperatures. During drilling operations, the mud temperature fluctuates due to its thermal interaction with the surrounding environment, which is typically hotter. This variability is particularly pronounced during activities such as connection and tripping, when mud circulation and downhole measurements are unavailable. Estimating temperature distribution along the wellbore before deploying costly downhole tools is critical to mitigate the risk of failure. Furthermore, developing an effective strategy to cool the mud relies on factors including circulation rate, duration, and inlet mud temperature.
In this study, we introduce an approach that combines physics-based modeling and machine learning techniques to achieve real-time prediction of mud temperature distribution. This method aims to enable precise and continuous estimate of mud temperature along the wellbore, facilitating more efficient thermal well management. An automated calibration system tailored for adjusting parameters within the physics-based hydrothermal model was also developed. This calibration process is designed to enhance the accuracy of the model and, further improve the performance of the monitoring system. The calibration system is smartly triggered by Discrete Event Simulation (DES) technique as and when operational conditions change on the rig. The advisory system synergizes with the monitoring system to suggest optimal mud circulation durations and flow rates. These recommendations are tailored to the inlet mud temperature, thereby ensuring precise control over the targeted temperature profile within the wellbore.
Our approach has been validated using select cases from the Utah Forge dataset for which wellbore temperature measurements were available. Our real-time monitoring system was able to estimate the mud temperature profile along the wellbore after prolonged stagnation of mud inside the wellbore due to other operations like connection and tripping when bottom hole mud temperature measurements were absent. The automatic calibration technique proved efficient in updating uncertain model parameters to provide improved predictions. Ultimately this approach can drastically improve temperature monitoring and management during the construction of a geothermal well and reduce tool failure.